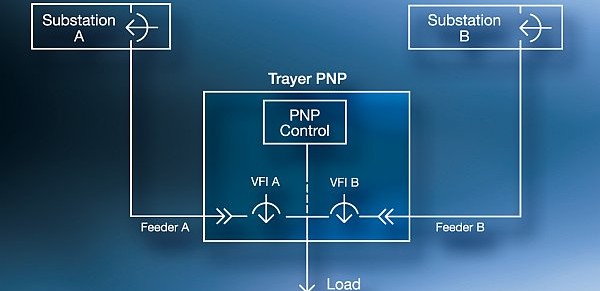
Press Release: Trayer Switchgear PNP Series
January 28, 2014Solid Dielectric Option Availible
February 2, 2018Why the Vacuum Load Interrupter?
For over forty years, the electrical industry has adopted vacuum contacts as a means of interrupting current flow in high voltage circuits. Vacuum contacts can interrupt high voltages with contacts moving only 1/4” or 3/8”. With this capability, smaller, low power mechanisms can replace mechanisms with huge springs and large operating power requirements. Electrical current cannot flow across a gap between two conductors unless there is a conductive path. A vacuum has no conductive path and thus it is an excellent insulator. Metallic contacts in a vacuum carrying current can be parted and the current will stop. Contacts parting only 1/4” will reliably interrupt load in circuits over 25,000 volts and have an open gap B.I.L. of 95 kV. Contacts parting 3/8” will reliably interrupt load circuits over 35,000 volts and have an open gap B.I.L. of 150 kV. Reliable interruption will occur for capacitor circuits or low power factor inductive circuits, and for any type of load power factor in between. Modern vacuum load interrupter contacts have an extremely long life without excessive contact erosion. A life of 10,000 or 20,000 operations is common.
In the early days of vacuum switching in power circuits, the industry discovered certain problems associated with their use:
1) The switches were too efficient. The switches would force the current to zero immediately upon contact parting, with current actually going from a high value to zero in micro seconds. This posed no particular problem in capacitive circuits, but in inductive circuits the inductance would give an induced voltage rise trying to maintain the constant flow of current. As a result, this “inductive kick” in voltage would produce severe transient voltages which would flash over insulators and cause insulation damage.
2) It was discovered that in some cases after years of use the vacuum would deteriorate due to the migration of the helium from the atmosphere outside into the glass envelope of the vacuum switch, through the molecular structure of the glass. This would spoil the arc interrupting capabilities of the switch once a sufficient amount of helium had been accumulated inside.
During the 1960’s advances in vacuum load interrupter technology were made. Original vacuum contacts were made of tungsten, because it was the only material which did not “outgas” in a vacuum. These contacts were replaced with copper-tungsten contacts that also do not “outgas” and they have the very desirable characteristic of not cutting off current flow abruptly as follows:
When the contacts begin to part the current initiates an arc that melts a microscopic puddle of copper on the negative contact or electrode (cathode). Molten copper ions then carry the full current across the gap to the other electrode (anode) and are deposited there. The current reaches a natural zero as the voltage polarity changes as the voltage waveform passes through the zero point. With no current flowing there is no further melting of the copper to provide an ion source, and no current flows during the next half cycle. When the voltage polarity reverses again (after another 1/2 cycle) the melt has stopped, current is zero and remains at zero. The contact always interrupts at current zero, and no voltage spikes are generated.
The process of solving this problem produced a contact that was almost totally transient free, and far superior to any other type of circuit interrupter. Until the introduction of vacuum technology “antique” switchgear broke a circuit path with simple blade contacts immersed in oil or gas. Oscillograms of oil or gas interrupters show noisy, spiky waveforms during interruption, not normal sine waves of currents and voltages. An analysis of the source of these waveforms reveals that during the time of contact parting, and until the arc is extinguished, the gap between the contacts is filled with a turbulent mixture of ionized and un-ionized gas or fluid. When the contacts first part the arc initiates and sets up an ionized path for the electrons. When the contact separation has been completed, there is no ionized path for the electrons. In between those two extremes, a turbulent mixture is present inside the bottle that results in rapid conduction fluctuations. During one microsecond there is a good conduction path, and during the next microsecond none, as if it had become an insulator.
The on/off conduction fluctuations between the two extremes occurs rapidly as the turbulence flips between ionized and non-ionized states. This results in a noisy voltage waveform with high voltage peaks one microsecond, lows the next, highs the next microsecond, etc. resulting in a high-frequency noisy signal. It’s like turning a switch on and off extremely rapidly. Every time these rapid voltage peaks go from high to zero, high to zero, and so on, the inductance in the circuit (wires and loads) tries to maintain a normal current during the “off” fluctuations by producing voltage “kicks”. The “inductive kick” phenomena results in spike-shaped high peak-voltage surges, commonly known as “switching surges”. These high voltage surges can be damaging to insulators and other elements in the distribution system. As switching surges travel down a distribution circuit and meet open connections or dead ends, they will reflect and travel back with double magnitude. When they meet other surges traveling in the line, they will either subtract from or add to other surge magnitudes.
In summary, the Trayer vacuum load interrupters produce pure sine wave voltages and currents during load interruptions, and do not introduce switching surges. Only in rare cases of interrupting unloaded transformers, where the current is so low as to not heat the electrode, is any noise fluctuation observed. Even this is limited to a few amps, which is harmless! If one can envision distribution systems being totally underground, then such systems will be totally shielded from lightning surges. If all switching is done with vacuum switches the other major source of surges on the system is eliminated by using vacuum technology. In this scenario, the system insulation would be free of one of its most common causes for failure, since in underground distribution INSULATION is the weakest link. High reliability would be achieved by those utilities willing to insist on all vacuum switching. (Interestingly, now the surge generation problem has been eliminated in switchgear it has drawn attention to other switching devices that create surges, with no remedies!)
The problem of gas migration through the envelope was solved by the development of a ceramic envelope to replace the glass envelope – like a bottle. This ceramic envelope is made of a cylinder of aluminum oxide, having metal ends formed as a part of the ceramic with a molecular bond. To complete the envelope, the stationary and moving contact assemblies, made of metal, are silver soldered to each end. Since the soldering operation is subject to the possibility of imperfect sealing, a testing technique has been developed. Following fabrication of each serially numbered unit, a carefully calibrated amount of A.C. voltage is applied. Any resultant leakage current is roughly proportional to the number of gas ions present in the tube. The leakage current for each serially numbered unit is recorded immediately and then again after the units have been shelved for a week. Any defect in the sealing will show up as an increase in the leakage current of the unit and it will then be re-worked or scrapped. Using this testing procedure and modern materials, space age reliability has been achieved. In fact, the finished bottles are more reliable than any linkage that can be used to operate them!
Vacuum contacts, with an appropriate mechanism, immersed in a dielectric medium such as oil or SF6 gas to reduce the necessary clearances between live conductors, buswork etc., creates very compact switchgear. Since the (brief) arcing is in a vacuum bottle there is no danger of the arc going phase-to-phase, or to ground. Also, the oil never burns (or carbonizes) during interruption since it is never subjected to an arc; the arc occurs inside a sealed vacuum bottle. This is a far safer approach compared to conventional oil switches that use crude blade contacts that separate, not in a vacuum, but in an oil dielectric medium. As the oil blades separate an arc will form and will only extinguish once the contacts have parted a sufficient distance, which could take several milliseconds. Until then, as the arc flows through the oil, it contaminates the oil with carbonized (burnt) oil. Over time, with successive operations, the oil becomes more and more contaminated. The accumulated carbon particles reduce the dielectric strength of the oil and can introduce a conduction path that makes the dielectric more flammable, more dangerous. Vacuum technology switchgear eliminates this hazard; the oil remains pristine and uncontaminated. Similarly in SF6 gas filled switchgear, arcing in gas can produce toxic by-products. With older blade switches as part of routine maintenance the oil or gas dielectric must be sampled periodically and contaminated oil or gas must be replaced. With a Trayer design, the switchgear enclosure (or tank) is hermetically sealed so that the oil or SF6 can never be contaminated by external leaks or ingress. Vacuum technology eliminates contamination from arcing since the arc is contained in a bottle, thus eliminating the burden of maintenance otherwise required for older, non-vacuum type switchgear.
In summary, modern vacuum switches will interrupt many times their continuous load current rating and can be applied for switching capacitors or to switch any type of load including highly inductive loads; they are not critical with regard to load power factor. Unlike all other types of switches modern vacuum contacts interrupt all circuits without generating switching surges which stress electrical distribution infrastructures and system insulation. Vacuum contact technology is safer, more reliable, requires less maintenance, and reduces the size of switchgear. It’s no mystery therefore why vacuum technology is so prized by the electric utility industry!